

In principle, we can always experimentally determine the VLE data we require. ( 2-1) and ( 2-2) in the design of binary flash distillation systems, we must take a short tangent and first discuss binary vapor-liquid equilibrium (VLE).Įquilibrium data is required to understand and design the separations in Chapters 1 to 15 and 17. For a binary system the mole fraction of the more volatile component in the vapor y and its mole fraction in the liquid x and T drum can be determined from the equilibrium expressions: Then vapor and liquid are in equilibrium. We will assume that the flash drum shown in Figure 2-1 acts as an equilibrium stage. In both cases we solve for flow rates, compositions, and temperatures before we size the flash drum. In the simultaneous solution method, all equations must be solved at the same time. In the sequential procedure, we solve the mass balances and equilibrium relationships first and then solve the energy balances and enthalpy equations. For the flash chamber, we can use either a sequential solution method or a simultaneous solution method. Of the remaining, the designer will usually select firstĪ number of other variables are available to fulfill the last degree of freedom.Īs is true in the design of many separation techniques, the choice of specified design variables controls the choice of the design method. Usually, the original feed specifications take up four of these degrees of freedom:įeed composition, z (mole fraction of the more volatile component) The designer has six degrees of freedom to work with for a binary separation. If the feed is already hot and/or the pressure of the flash drum is quite low, the pump and heater shown in Figure 2-1 may not be needed. The pressures must be chosen so that at the feed pressure, p F, the feed is below its boiling point and remains liquid, while at the pressure of the flash drum, p drum, the feed is above its boiling point and some of it vaporizes. In addition, he or she will need to know how much the original feed has to be pressurized and heated. He or she also wishes to know the pressure, temperature, and flow rate of the feed entering the drum. The designer of a flash system needs to know the pressure and temperature of the flash drum, the size of the drum, and the liquid and vapor compositions and flow rates. Figure 2-1 shows a vertical flash drum, but horizontal drums are also common. Because of the intimate contact between liquid and vapor, the system in the flash chamber is very close to an equilibrium stage. The system is called “flash” distillation because the vaporization is extremely rapid after the feed enters the drum. A demister or entrainment eliminator is often employed to prevent liquid droplets from being entrained in the vapor. The vapor is taken off overhead, while the liquid drains to the bottom of the drum, where it is withdrawn. Because of the large drop in pressure, part of the fluid vaporizes. The fluid is pressurized and heated and is then passed through a throttling valve or nozzle into the flash drum. The equipment needed for flash distillation is shown in Figure 2-1. Usually a large degree of separation is not achieved however, in some cases, such as the desalination of seawater, complete separation results. The more volatile component will be more concentrated in the vapor. In this process, part of a feed stream vaporizes in a flash chamber, and the vapor and liquid in equilibrium with each other are separated. One of the simplest separation processes commonly employed is flash distillation.
When to use depriester chart plus#
Aspen Plus Troubleshooting Guide for Separations
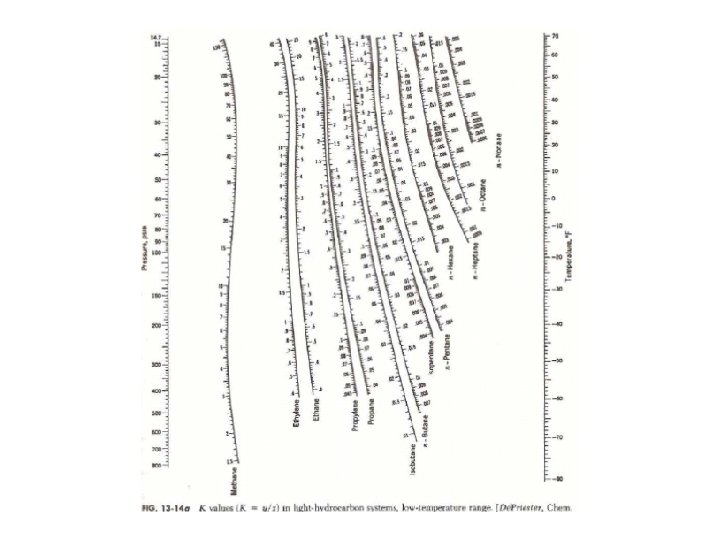
Chapter 2: Flash Distillation by Phillip C.
